Wyroby ceramiczne znane są od tysięcy lat. Ceramika to sprawdzony materiał, który otacza nas każdego dnia, nie tylko na produktach codziennego użytku, ale także w miejscach, w których można się tego nie spodziewać.
Jednym z takich obszarów są systemy kominowe, w skład których wchodzą również ceramiczne wkłady kominowe. Mówiąc najprościej, są to rury, które układają się jedna na drugiej, tworząc rurę kominową, w której spaliny są odprowadzane z kotła. Wkładki ceramiczne to mocny i bardzo odporny materiał, który znosi działanie ciepła, dymu, sadzy, ale także wody i mrozu.
Jak powstają ceramiczne rury?
Podstawą każdego wyrobu ceramicznego są surowce naturalne – iły, gliny, które są mieszane z grubszymi cząstkami tzw. materiałem schudzającym. Materiał schudzający lub kruszywa mogą być naturalne, lub nawet sztucznie wytworzone, a ich właściwości zasadniczo wpływają na końcowe właściwości produktu. Nie brak w nich również dodatków, które przyczyniają się do korekty w celu uzyskania wymaganych parametrów. Wszystkie składniki miesza się w odpowiednich proporcjach i dodaje wodę, aby uformować plastyczne ciasto. To ciasto jest następnie wytłaczane przez prasę ślimakową, która jest praktyczną gigantyczną maszynką, jak maszynka do mielenia mięsa. Wielkość i kształt produktu określa otwór, przez który z prasy wychodzi nieograniczone co do długości pasmo masy, długość produktu jest dowolna, a poszczególne kawałki są cięte automatycznie, najczęściej za pomocą stalowej struny.
W efekcie otrzymujemy więc wytłoczoną rurę, która jest wystarczająco mocna, aby poddać ją dalszej obróbce, ale nadal łatwo się odkształca. Najpierw musimy usunąć wodę z produktu. Produkty możemy suszyć w temperaturze otoczenia lub skorzystać z suszarni. Jednak po wyschnięciu nadal można łatwo połamać rury i zmiażdżyć je rękoma. Dopiero wypalenie nadaje ceramice ostateczne właściwości. Podczas wypalania poszczególne składniki stopniowo reagują, tworzą się nowe fazy mineralogiczne, a produkt krzepnie. Na końcu pieca otrzymujemy finalny produkt ceramiczny. A jak taki proces przebiega w praktyce?
Bezpośrednio po wytłoczeniu poszczególne kształtki układane są w kilku warstwach na tzw. wózki piecowe. Celem jest maksymalne wykorzystanie powierzchni wózka piecowego. Pomiędzy poszczególnymi kolumnami rur muszą pozostać małe szczeliny, aby gorące powietrze wewnątrz pieca mogło przepływać we wszystkich kierunkach między wszystkimi produktami. Zapewni to równomierne wypalanie całej zawartości wózka piecowego. Wózki piecowe wprowadzane są kolejno do pieca tunelowego o długości około 200 m. Cykl czasowy przesuwu wózków piecowych zmienia się w zależności od wydajności produkcyjnej i trybu wypalania, najczęściej wynosi około 60 – 180 minut. Przejazd przez piec tunelowy, w zależności od jego długości, trwa kilka dni, maksymalna temperatura w piecu wynosi około 1100 °C dla tego typu ceramiki.
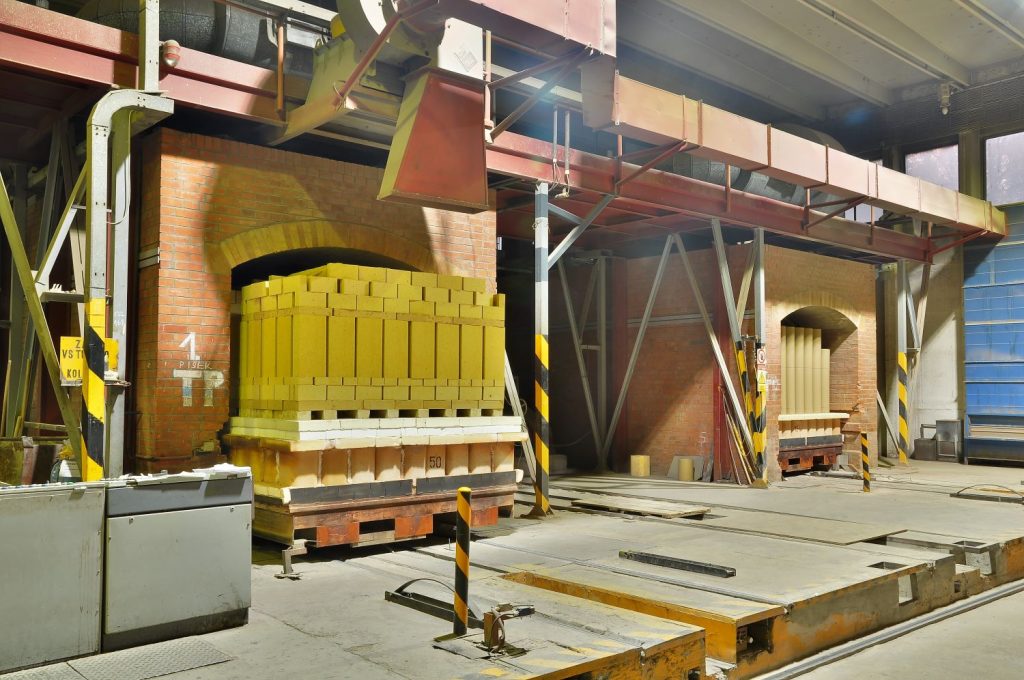
Po wypaleniu następuje kontrola jakości, pracownik najpierw ocenia wygląd kształtek, mierzy wymiary, aby ocenić wymagane tolerancje i owalność. Druga część kontroli odbywa się w laboratorium, gdzie określany jest skład chemiczny, wytrzymałość, porowatość, odporność na szoki termiczne czy odporność na kwasy.
Po spełnieniu wszystkich wymagań towar jest gotowy do wysyłki, rury są układane na paletach i mocowane z użyciem taśm i opakowań ochronnych. Teraz pozostaje tylko dostarczyć towar do klienta.
Autor artykułu: Ing. Lucie Keršnerová, Ph.D., Head of R&D, P-D Refractories CZ a.s.
Tu znajdziesz kominy na lata. Poznaj naszych partnerów